Table of Contents
While we’re living in a time when technology is seeping in everywhere, making processes more straightforward, and keeping everything connected, many organizations are still reluctant to modernize their maintenance management approach. These organizations are still debating about the famous maintenance management topic – preventive vs. reactive maintenance, and whether moving towards the preventive approach will be as good as everyone makes it out to be.
While organizations still using reactive maintenance might be worried about the costs, learning curve, and the ROI of preventive maintenance (PM), the benefits far outweigh the costs. That being said, let’s dive deep into preventive vs. reactive maintenance, why the former is better, and how a robust CMMS software solution helps with it.
What is the difference between preventive vs. reactive maintenance?
To understand the difference between preventive and reactive maintenance, one needs to understand both.
Reactive maintenance in a nutshell
Reactive maintenance is an age-old approach – it allows the pieces of equipment to operate as needed until they malfunction. Then, after the equipment fails, technicians fix it to bring it back to its original state. While this might seem cost-effective and straightforward to many, the truth is the polar opposite.Â
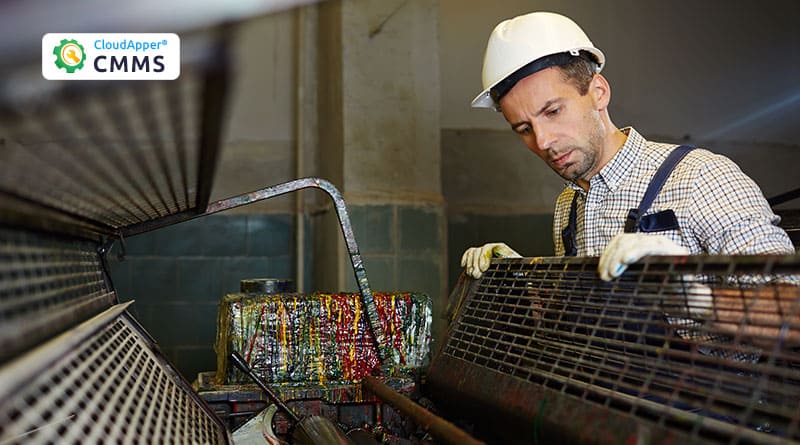
Fewer resources, time, and costs are required for reactive maintenance, but the drawbacks are too significant to ignore. For example, let’s consider a piece of equipment – a lathe machine. It requires maintenance activities such as lubrication, cleaning, checking its driving belts, spindle tapers, etc. With reactive maintenance, none of that is typically done, and the machine will operate without receiving any care until it fails. However, every time it gets maintenance after it fails, it’ll become inefficient over time due to more wear and tear, overheating, and other problems – leading to reduced longevity, unplanned downtime, and even workplace safety incidents.Â
Reactive maintenance is applicable for more straightforward equipment like light bulbs, but it’s unfeasible when it comes to complex, expensive, and heavy machinery like a lathe machine. This maintenance approach only addresses problems after they arise and doesn’t prevent the problems right from the start. Modern plants consist of machinery and pieces of equipment that require constant maintenance to operate reliably, last longer, and reduce disruptions – that’s precisely what preventive maintenance does.Â
Preventive maintenance in a nutshell
Preventive maintenance is the most balanced and famous approach to maintenance management. It works by preventing the problems right off the bat, and by doing so, reduces unexpected equipment breakdown, improves the longevity of assets, and reduces maintenance costs down the line. In addition, everything is planned with preventive maintenance, which makes it a more organized, controlled, and practical approach.
Let’s talk about the lathe machine once again – it requires maintenance to operate optimally. With preventive maintenance, the machine is lubricated when necessary. Inspections are conducted to check whether the driving belts, spindle tapers, or any other parts are worn out, and it’s cleaned accordingly.
The pieces of equipment get the maintenance required to keep them running smoothly – this helps maintain performance, makes the machinery more reliable, and helps them last longer.Â
While preventive maintenance might have higher initial costs, it does reduce replacement, repair, and maintenance costs down the line. For instance, these pieces of equipment are quite expensive, and replacing one due to premature death can strain the finances of any given organization. Preventive maintenance, on the other hand, is far cheaper than replacing assets that have died prematurely.
Why is preventive maintenance better than reactive maintenance?
Whenever the topic of preventive vs. reactive maintenance comes up, the clear winner is the former.
Preventive maintenance uses more technicians, maintenance management software, careful planning, support from the management, and effective collaboration that helps the equipment run smoothly, reduce malfunctions, minimize workplace safety incidents, and simplify repairs.
Reactive maintenance, unfortunately, does none of the above, and it simply isn’t applicable for most pieces of machinery nowadays.Â
But what benefits does preventive maintenance bring to organizations that utilize it?Â
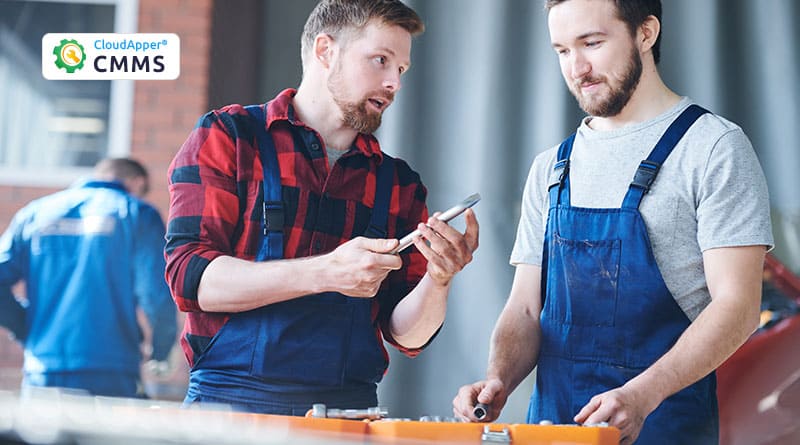
What are the benefits of preventive maintenance?
There are several benefits of utilizing preventive maintenance, and the experience might vary from one organization to another. However, some of the most common benefits of preventive maintenance are given below.
- It reduces unexpected equipment downtimeÂ
- It reduces major repairs
- It extends asset life
- It reduces premature equipment replacements
- It improves workplace safety
- It improves productivity by minimizing major disruptions
- It identifies even the smallest issues with equipment and helps address themÂ
- It helps plan downtime in a way that doesn’t hamper operations
- It increases savings as replacement, repair, and maintenance costs are reduced
Shifting towards preventive maintenance is just a part of the process – maintenance managers need the right tools, plan, personnel, and systems to help them with it. Fortunately, CloudApper CMMS can help maintenance managers streamline maintenance efforts.
Shift to preventive maintenance with CloudApper CMMS
CloudApper CMMS is a modern, robust, and affordable CMMS software that streamlines maintenance efforts, simplifies repairs, and improves collaboration. It is the perfect tool for preventive maintenance – it ensures asset management, spare parts and inventory management, technician management, vendor management, and much more.
CloudApper CMMS is built with CloudApper, a no-code platform for enterprise mobile app development, and thanks to that, the maintenance management app is entirely customizable by users! Instead of adjusting the maintenance workflow to fit the solution, managers can modify the app themselves to fit their workflow, making it a must-have tool for your maintenance management efforts.Â
CloudApper CMMS is only $10/user/month and provides access to a plethora of mobile enterprise apps thanks to CloudApper’s marketplace. Contact us today and see how it helps with your preventive maintenance efforts.Â
What is CloudApper AI Platform?
CloudApper AI is an advanced platform that enables organizations to integrate AI into their existing enterprise systems effortlessly, without the need for technical expertise, costly development, or upgrading the underlying infrastructure. By transforming legacy systems into AI-capable solutions, CloudApper allows companies to harness the power of Generative AI quickly and efficiently. This approach has been successfully implemented with leading systems like UKG, Workday, Oracle, Paradox, Amazon AWS Bedrock and can be applied across various industries, helping businesses enhance productivity, automate processes, and gain deeper insights without the usual complexities. With CloudApper AI, you can start experiencing the transformative benefits of AI today. Learn More